Don’t Get Caught With Your Walls Down
Use Prefabricated Wall Panels and Floor Systems
One of the greatest advantages to using prefabricated building components and prefabricated wall panels is simultaneous construction. While your grading and foundation crews are working, so are we.
At Pacific Wall Systems, performance is not limited to weather, daylight, city noise ordinances, vandalism, or other on-site challenges. Therefore, you can depend on a seamless construction schedule without the wasted time and material.
In addition, assembling the frame components in a controlled environment allows us to deliver a superior product.
How We Roll:
We Provide:
- Competitive, accurate bids – commercial and residential.
- Professional design and layout of your plans.
- Precision built wall panels and floor systems delivered to your site.
- Panel layout plan for a clear path to success.
- Technical support throughout your project.
- Finest quality lumber.
- On time delivery.
- Plant tours available.
Manufacturing the dream — all wood in the ’hood
Prefabricated Wall Panels
The Oregonian OregonLive.com October 16, 2023
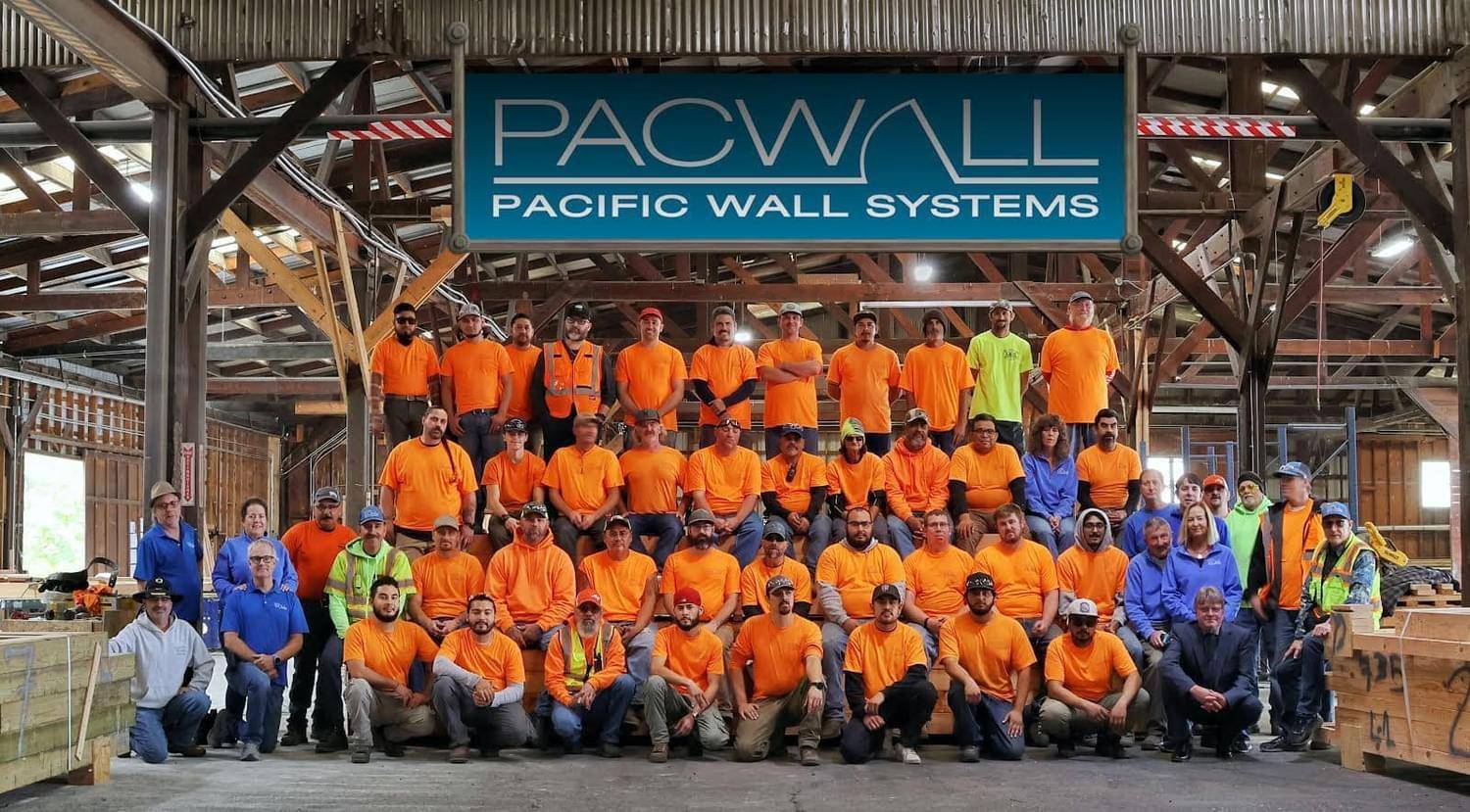
As the housing shortage crisis intensifies across the nation, the need for affordable, efficiently built, single and multi-family homes using sustainable building practices is paramount. Two Oregon companies, Pacific Wall Systems, and Wood Mechanix, have joined forces to meet that challenge through off-site component building that deploys zero waste through best practice business models that also engage the local communities for which they build.
Established in 1978, family-owned wood framing specialty contractor Wood Mechanix is headquartered in Portland and employs a steady workforce of 165 carpenters. When you see a crane in the Portland area, chances are it’s a Wood Mechanix project!
Established in 2007 and headquartered in Phoenix, Oregon, Pacific Wall Systems, Inc is a women-owned entity headed up by Konny Knecht, President and CFO, with a team of 90 ranging from carpenters to CAD designers with two manufacturing facilities proudly serving Oregon, Washington and California.
Manufacturing and delivering wood building components off-site in a controlled environment.
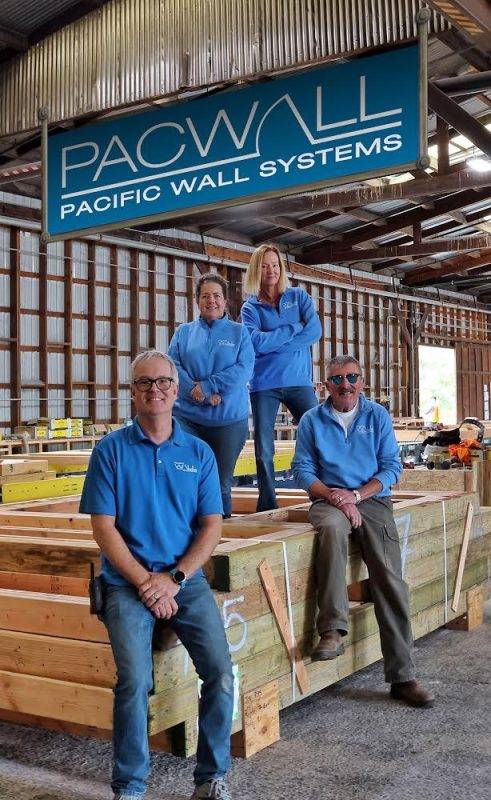
According to Nancy Mansfield, Director of Marketing, it all began in 2006 when her brother Alex Knecht, a general and specialty contractor, started to research and develop a business model that focused on manufacturing and delivering wood building components off-site in a controlled environment. He then pitched his idea to start a family-owned company in Southern Oregon. Having witnessed most commercial construction being manufactured offsite in the Midwest and the East Coast, Knecht wanted to bring that technology to Oregon.
Portland-based Wood Mechanix saw the value in this efficient, cost-effective off-site manufacturing practice and that this system could remedy restrained and schedule restricted jobsites. Hence a partnership with Pacific Wall Systems was born.
“Here on the West Coast, with the exception of trusses, very few contractors were using off-site building components,” said Mansfield. “Our association with Wood Mechanix became very synergistic.”
Prefabricated walls increase efficiency and productivity while reducing waste.
Both companies agree that traditional stick framed buildings can create wasted lumber. Instead, prefabricated walls increase efficiency and productivity while reducing waste. Off-site component building is also not restricted by noise ordinances, weather, or labor shortages. Additionally, with real estate in high demand and lot sizes shrinking, the ability to store lumber and stick frame on site can become logistically challenging and at times impossible.
“The beauty of wall panel manufacturing — where we shine — is on large commercial housing projects where the time value of money is an important part of the economic model, and also creates a seamless production schedule for our customers. Design process and completed wall assemblies can be started before the concrete subcontractors have finished. It’s not only a huge time saver but the customer saves money on labor costs as well.” said Mansfield.
How does this benefit the affordable housing market?
Indoor wall manufacturing takes full advantage of lean, efficient automation thus reducing labor costs and hands down is quicker and cleaner to erect on the job site.
“Our system is a perfect fit to address the affordable housing market and we are expanding our operations to meet the housing crisis in Oregon.” said Mansfield.
How is off-site building cleaner? By using, reusing and repurposing 100 percent of the lumber, Pacific Wall Systems prides itself in contributing little to nothing to the landfill.
Believing in the full circle concept when it comes to utilizing raw materials; both companies appreciate lumber as a renewable resource — and none of it needs to be wasted.
“Every day we put huge bins of scrap lumber out for people to take,” said Mark Mansfield, Logistics Manager. It burns beautifully to heat homes or even facilitate hobbies. Our local fire chief whittled pieces into animals and toys and delivered them to the children’s hospital.”
“We could talk all day about the nuts and bolts of the business — how many linear feet of walls we produce a day, job costing, logistics and the like,” said Mansfield. “But at the end of a long workday, the satisfaction of what we do lies in two main realities: witnessing our employees better their lives through their hard work and bringing a paycheck home to their families and seeing our communities be able to build affordable homes and, if needed, heat those homes. This is what it looks like to be responsible manufacturers. This is the dream that warms the heart, hearth and home.”